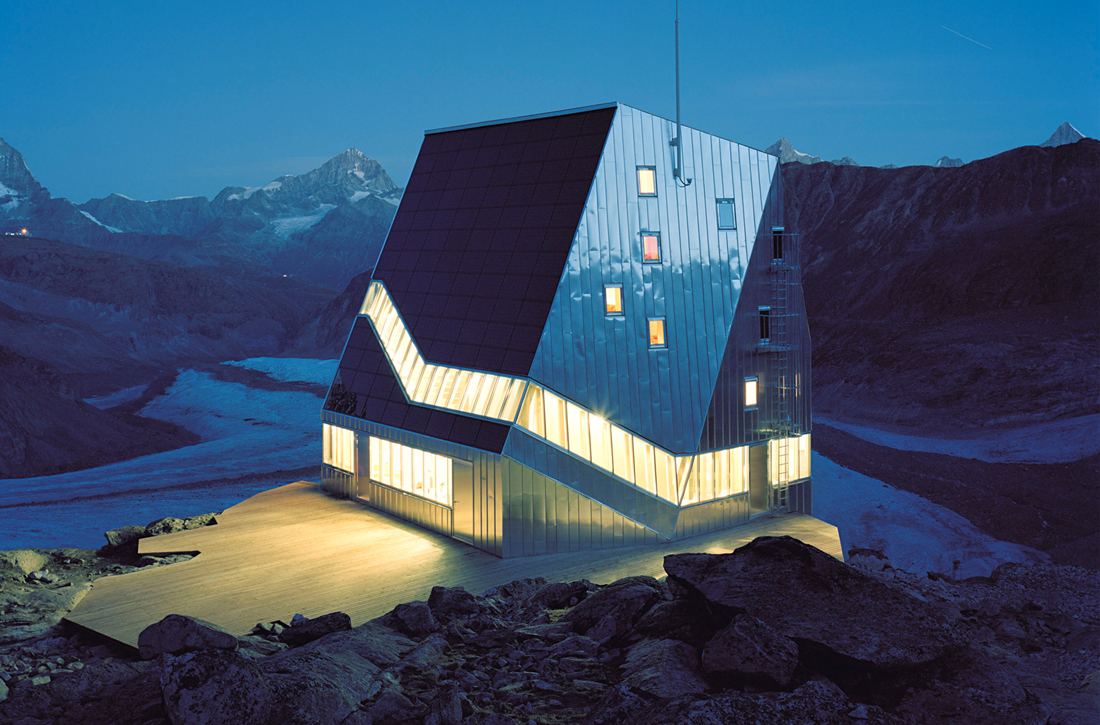
PROJECT INFO
Building type:
Hotels
Year:
2009
Project Status:
Built
Gross Area:
698 Sqm
Certificates:
Climatic zone:
Extreme Cold
MY LAST SEEN PROJECTS
PROJECT DESCRIPTION
2,883m above sea level, inaccessible by car or ski lift and a three-hour hike from the base of the mountain, the Neue Monte Rosa-Hütte is a destination for only the most dedicated architecture fans. The lodge and restaurant for Swiss hikers, on the icy slopes of the Monte Rosa mountain in the Swiss Alps. The building results from a successful collaboration between Bearth&Deplazes architects, the ETH of Zurich and the Swiss Alpine Club (SAC).
Contemporary version of a medieval donjon: Five-story wood construction made from prefabricated frame elements. The isolated mountain location mandates the greatest possible self-sufficiency.
The ambivalence between a sense of security and being exposed defines the building’s structure: below are the communal areas with surrounding ribbon glazing, above the closed sleeping quarters. The cascading spiral stairway opens panorama views when ascending, follows the course of the sun, captures the solar irradiation, and distributes the warmth of the sun throughout the entire house.
AWARDS
SUSTAINABILITY FEATURES
Ventilation + Heat recovery
Passive Solar
High efficient façade
Photovoltaics
Rainwater harvesting
Sustainable sourced timber
Smart design (passive design strategies)
Zero energy building
Daylighting maximised
SUSTAINABILITY STRATEGY
MATERIALS AND CONSTRUCTION TECHNIQUE
- Foundation: 40 rock anchors, central shear hub and ten individual foundations of concrete
- Steel construction: Steel "table" (platform) with 10 star-shaped axes, galvanised
- Timber construction: Five-storey timber element building
- Insulation: Mineral insulation with insulation uprights, thickness 30 cm, U value building envelope 0.11 W/m2K
- Façade and roof: double-standing seam, aluminium sheeting, uncoated
- Ribbon window: Post-and-beam construction, uncoated aluminium, triple glazing, Ug value 0.7 W/m2K, Uw value
1.2 W/m2K, g value 0.27 to 0.50, depending on orientation
- Photovoltaic façade: Post-and-beam construction, anodised aluminium; made-to-measure photovoltaic modules,
laminated safety glass, black enamelled
- Windows: Skylights pine, triple glazing, Ug value 0.5 W/m2K, Uw value 1.0 W/m2K, g value 0.45, external
surround titanium zinc, frame uncoated aluminium
-External doors: Metal, uncoated aluminium
- Escape ladder: metal work, galvanised steel
- Stairs: Cascade stairs, solid oak, untreated; stairs warden solid beech and spruce, untreated
- Floor finishes: 1st basement, washrooms and toilets polyurea, black; dining room: floorboards spruce/fir, oiled; circulation areas, dormitories and warden’s apartment kugelgarn carpet, white poplar.
- Walls: Open frame and trusses ground floor three-ply panels and members spruce/fir, untreated; open frame 1st
to 3rd floor three-ply panels and members spruce/fir, untreated; cladding 1st basement, circulation area and kitchen: plasterboard, some areas painted
- Ceilings: Ground floor, 1st to 3rd floor three-ply panels spruce/fir, untreated, cladding 1st basement, circulation area and kitchen plasterboard, some areas painted
- Internal doors: Door frame with integral architrave, on one side solid oak, door leaf MDF, painted
- Joinery: Beds and storage areas solid ash with brown core and three-ply panel spruce/fir, untreated; benches ash with brown core and three-ply panel spruce/ash, oiled; counter, buffet, cupboards and boot-racks three-ply panel spruce/fir, untreated; partition walls and signs wet rooms chipboard covered with laminate panel, water-resistant, black
- Joiner furniture: Tables and stools solid ash with brown core, oiled
- Sun protection: Blinds along ribbon window in dining room textile screen reflective, grey
- Colours: Public area 1st basement level, circulation area and doors acrylic paint, light gold; reveals to ribbon windows, warden’s stairs, counter and core with doors acrylic paint, silver
- Terraces: Stone-retaining walls; connection to terrain spruce/fir, untreated; substructure, grating and stairs larch, untreated; metal railing, galvanised
ENERGY AND BUILDING SERVICES
- Basis for calculations: 6'500 overnight stays and 2'000 day guests per year during main season.
- Water requirements: Fresh-water requirements 210 m3 per year, of which 57 m3 for the kitchen including dishwasher, 105 m3 for the washstands and hand washbasins, 30 m3 for the private and public showers, 18 m3 for cleaning; melt water collected during July and August; storage capacity for the other months when hut is in operation min. 160 m3
- Energy requirements: Heating energy requirements 17'500 kWh per year, area to be heated 899 m2; warm-water
requirements 3'500 kWh per year, 120 m3 per year; electricity requirements 9'900 kWh per year (without cooking), of which 2'300 kWh for waste-water treatment system, 2'300 kWh for lighting, 1'800 kWh for building services, 1'400 kWh for housekeeping, 2'100 kWh battery and distribution losses.
- Degree of self-sufficiency: 90 % energy self-sufficient, without cooking.
- Certification: Minergie-P, certificate VS-013-P
- Photovoltaic system: Photovoltaic system integrated in façade; 100 made-to-measure modules in 16 different forms, total area of modules 110.4 m2; glass-glass-laminate, 6 mm solar glass, toughened safety glass, and 6 mm float glass, toughened glass, with mono-crystalline solar cells 125 x 125 mm; total 16'056 Wp nominal performance (peak performance), angle of inclination 66.2º.
- Power storage: Compact-Power battery, battery voltage 48 V DC; 2 parallel strands, each with a capacity of 3'000 Ah
- Power inverter: Exploitation of maximum energy production of the photovoltaic system by Maximum Power Point
Tracker MPPT, OutBacks; conversion from 48 V DC to 230 V AC by 3 transfer systems Xtender consisting of power inverter 8'000 VA/230 V AC and battery charger 48 V DC as well as a power inverter 600 VA/230 V AC for the fire alarm system and the building automation.
- Lightning protection: Lightning protection with external lightning rod, 5 m above ridge, for complete protective shield.
- Solar thermal collectors: 24 high-performance flat collectors; filled with inert gas anti-reflex double glass and high selective
absorber coating, 2.52 m2 absorbent surface per collector, total 60.5 m2 absorbent area; orientation: south-west, inclination ca. 60°.
- Heat store: Combined storage tank with layer-loading facility and integrated drinking-water heater; heat store total 5'500 l; integrated warm-water storage tank 280 l
- Cogeneration plant: Run on rapeseed oil, synthetic diesel or biodiesel; electrical performance max. 12 kW, heating performance up to 27 kW with normal atmosphere.
- Heating: Use of passive-solar energy, remaining needs met from solar thermal collectors, air heating; minimum room air temperature when hut is in operation restaurant 15 °C, rooms 10 °C; target room air temperature when hut is in operation restaurant 20 °C, rooms 18 °C; during winter season min. 5 °C, frost protection; water heating by solar thermal collectors, 45 to 90 °C
- Ventilation: Central ventilation plant, flow rate 4'300 m3/h; alternating ventilation of the zones dining room or dormitories; need-related control by means of room air temperature and concentration of CO2 (zone dining room) or by occupancy switch (zone dormitories); central heat recovery, air heating if required, separate ventilation system in kitchen, flow rate 2'500 m3/h; outside air collection in gap beneath building (snow absorber) preheater for frost protection of the heat exchanger
- Water storage: Rock cavern with storage capacity of 200 m3, height difference of 40 m above the hut, natural geodetic pressure for appliances, insulated pressure pipe with frost-protection tape for emergency operation, thermal circulation with solar heat for frost safety, operating pressure 4 bar.
- Fresh-water supply: Coarse and fine filter as well as UV treatment, boiling up of solar preheated water for drinking water
- Waste-water treatment: Microbiological waste-water treatment plant with immersed synthetic flat membranes, pores >35 nm; total number of inhabitants and population equivalents TP 55; dry-weather feed QT 3.5 m3/d; biochemical oxygen requirement BSB5 3.3 kg/d; electrical connection 13 kW; temperature zone 10 °C to 30 °C; automatic addition of highly concentrated nutrient solution when load is low; coarse material and surplus slurry removed on site by bagging unit; effluent per year 310 m3; grey water per year 100 m3 for flush toilets and washing machines
- Kitchen equipment: Gas cooker with oven, gas-tilting bratt-pan fryer, gas combination steamer, 2 induction plates (used when surplus solar power available), dishwasher, refrigerator, deep-freezers
- High-voltage installations: Energy-efficient appliances, 230 V AC; 3 appliance groups with different priorities
- Low-voltage installations: Telephone, Internet, fire alarm system, coin-operated showers and building automation system
- Lighting: Fluorescent lamps with electronic ballast
- Meteo station: Equipment from MeteoSwiss, local climate data for building automation system
ENERGY DATA
Energy consumption:
N/A (N/A )
Consumption type:
Annual carbon footprint:
N/A (N/A )
Climate zone:
Extreme Cold
Min. temperature =
N/A
Max temperature =
N/A
RH =
N/A
CLIENT
Client:
SAC, Sektion Monte Rosa
DESIGNERS
Architect:
Architect:
ETH , Bearth & Deplazes architekten , Valentin Bearth , Andrea Deplazes , Daniel Ladner
CONSULTANTS
Manager:
Marcel Baumgartner , Architektur & Design GmbH
Specialist consultant:
WGG Schnetzer Puskas Ingenieure , Lauber Iwisa , ETH Digital Fabrication
Structural Engineer:
Holzbaubüro Reusser , SJB Kempter Fitze AG , Holzbau AG
CONTRACTORS
OTHER PROJECTS BY TEAM
SIMILAR PROJECTS
Via Giulio Romano, 00054 Fiumicino RM, Italia | 2018